Rocket Warhead Containment System (RWCS)
Our challenge was that the customer needed to re-design their existing Blue Grass Chemical Agent-Destruction Pilot Plant processes & equipment that had been built and dedicated to the disposal of M56 Warheads containing the nerve agents VX & GB. The solution, the Rocket Warhead Containerization System (RWCS), through a collaborative and iterative design process, the team redefined what was possible and invented a superior processing solution that addressed all the customer needs and gained a “best-practice” designation of teamwork and collaboration on the BGCAPP project.
This system, dubbed the “double-back flow” system, is a process that starts and ends at the canister skid station. A custom skid with empty, custom designed canisters and caps is conveyed to a robotic picking station, where they are removed from the skid and placed into a fixture attached to an Autonomous Mobile Robot (AMR). The AMR then transports the empty canister to a robot, where it removes the canister and passes it through an air lock to be received by another robot and placed into a custom designed crimping station and where it removes the canister cap. At this time, the warhead to be processed is conveyed from the orbital wrapper and is robotically picked from the conveyor and placed into the canister. The custom cap, designed to increase the efficiency of the destruction process, is then placed on the canister. The crimping station, which applies 30 tons of pressure, applies (2) crimps, which overlap to create a 360-degree seal that is airtight.
From the crimp station, the filled canister is then presented back through the airlock where it is weighed and labeled for tracking purposes. Upon completion of the labeling, a robot will place the canister back into an AMR where it is transported back to the skid station where it is placed in a finished canister skid. When the skid is full, it is conveyed out of the RWCS and is stored until ready for destruction. The process then continues, processing 25 warheads per hour, running 24-hours per day.
This multi-station solution resulted in a successful process that achieved a safer operating environment, increased productivity and opportunity for lower operating costs.
The RWCS consists of two complete systems, one for training and one for operation in the facility. This system is a combination of CRG designed and assembled components as well as the integration of products from our industry leading network of suppliers.
Components for this system include:
- 16 Industrial Robots
- 8 MIR-CRG Precision Docking Stations
- 2 Main Control Panels
- 16 EOAT Actuators
- 5 HMI Control Room Consoles
- 20 Conveyor Sections
- 16 Custom EOAT’s
- 4 Orbital Wrappers
- 8 Custom Reject Racks
- 16 Custom Robot Pedestals
- 4 Industrial scales
- 6 Custom Controller Racks
- 11 AHS-MIR-100 AMR’s
- 4 Custom Canister Scale Holders
- 4 Custom Canister Scale Holders
- 11 Custom Top Mount Modules
- 14 Printers
- 6 Barcode Readers
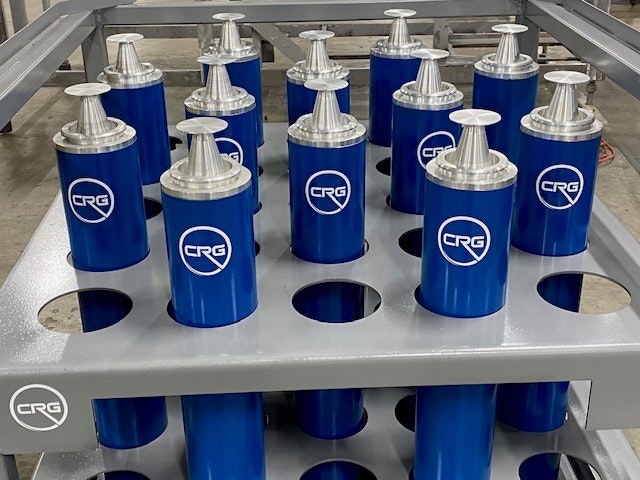
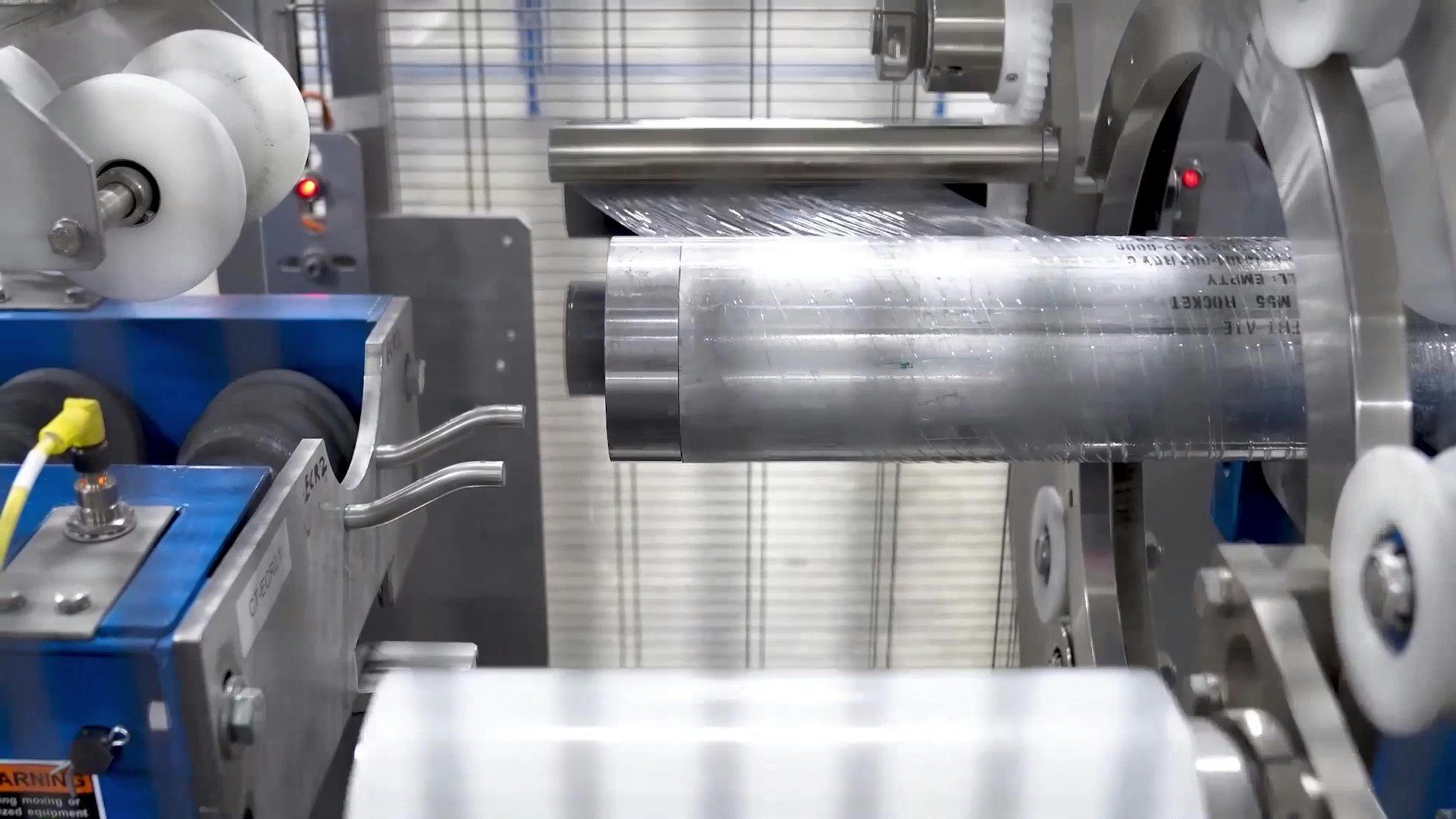
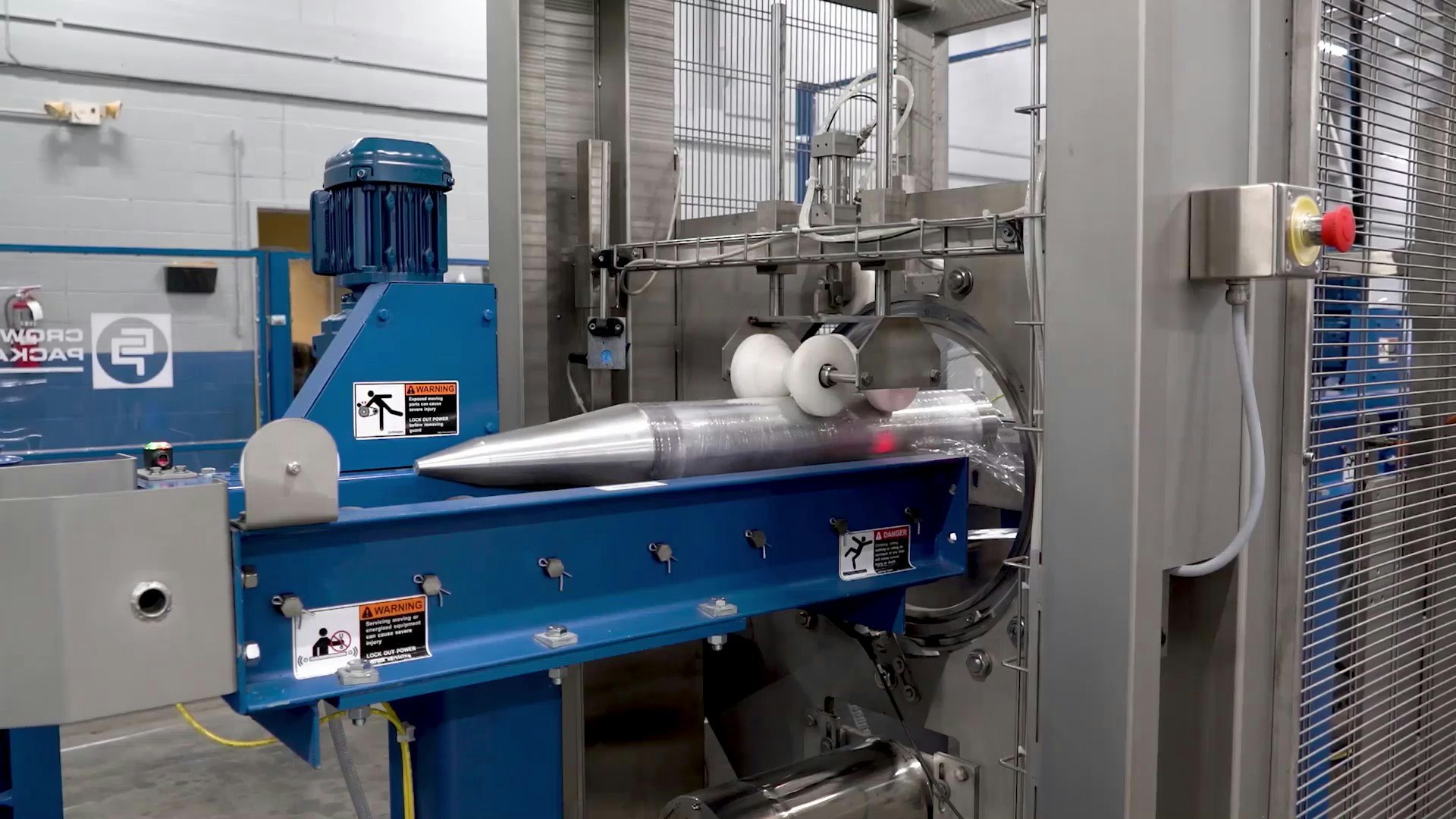