Custom Assembly & Manufacturing Automation Solutions
Overview
Custom Assembly & Manufacturing Solutions
CRG Automation’s team of experienced engineers and assemblers understand each assembly system is unique, and so are the issues that they face. We apply our wealth of industrial automation knowledge to create custom assembly systems that effectively address your project’s unique pain points. We delve into what’s keeping your facility from becoming more efficient and devise custom assembly and manufacturing solutions to streamline your process and eliminate bottlenecks. In other words, CRG Automation transforms your assembly issues into automated advantages with our custom manufacturing solutions.
Explore just a few examples below which demonstrate how CRG Automation has created unique, industrial automation solutions to complex issues that had our customers scratching their heads.
CRG Automation developed a custom robotic industrial automation system for the examination of M55 Rockets. The primary function of the RNDE System is to safely and efficiently examine the contents of an M55 Rocket contained in its original Shipping and Firing Tube via x-ray technology prior to processing the unit on the rocket line.
Features of this custom assembly system include:
- INPUT and OUTPUT Transport Carts
- X-ray Scanner & Detector housed in a leaded enclosure
- 2-Axis “Pick and Place” robot for material handling
- Servo Motion Sled with Tilting mechanism
- Safety Interlocks
- Operator Cart Control Panel

CRG Automation is pleased to present this video as an overview of a custom designed and built robotic cell that automates the dangerous and monotonous task of loading M56 chemical agent warheads that have been previously packaged and sealed in containers into a Static Detonation Chamber, or SDC, for their final destruction.
Features of this custom assembly include:
- Case Erecting
- Material handling
- Precision Packaging
- Conveyor system
- Robotic Handling
- Automated Labeling
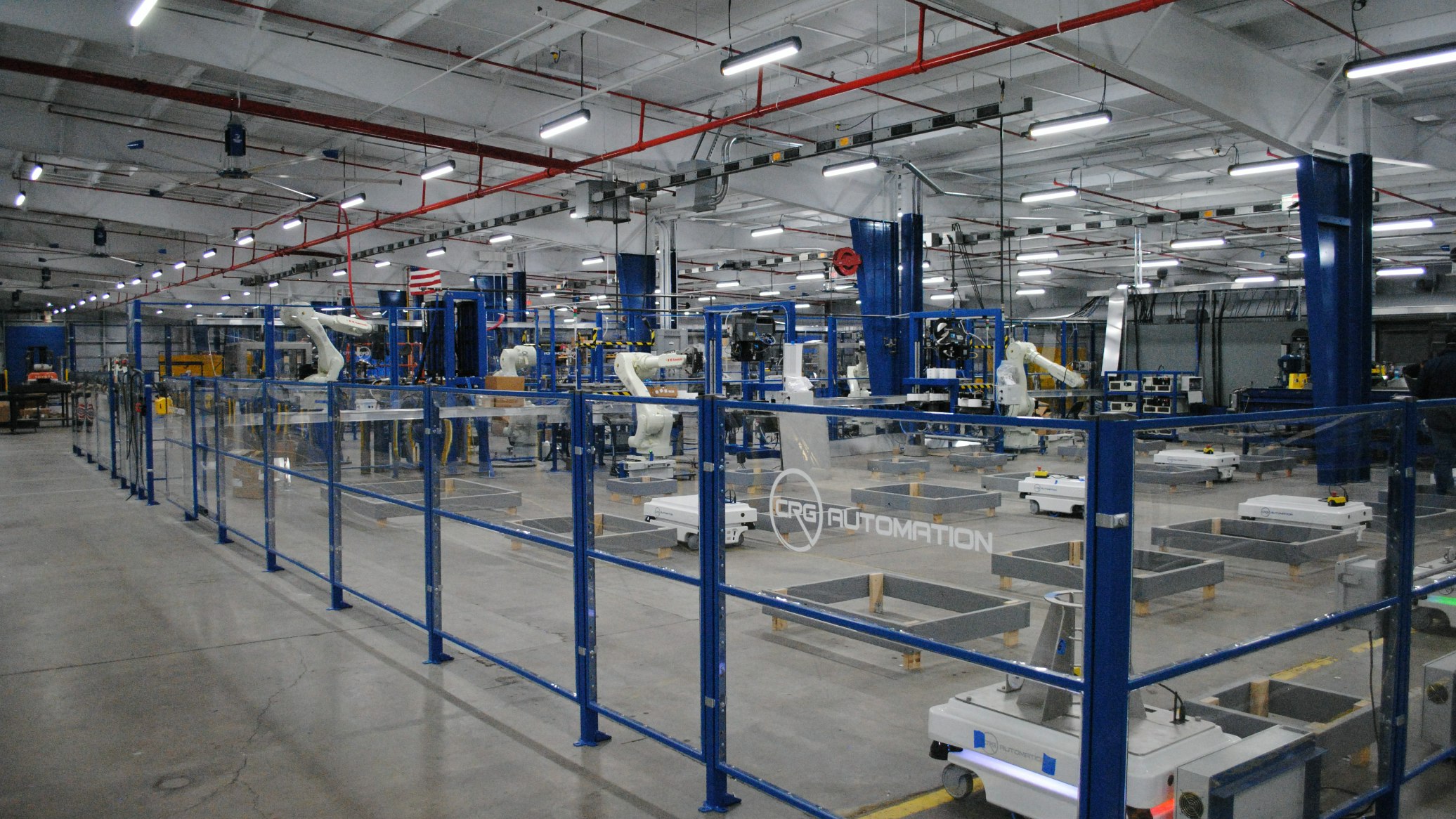
Through a collaborative and iterative design process, the CRG Automation team redefined what was possible through industrial automation and invented a superior processing solution that addressed all the customer needs. This multi-station solution resulted in a successful process that achieved a safer operating environment, increased productivity, and opportunity for lower operating costs.
Features of this custom assembly system include:
- Material Handling
- Precision Crimping
- Wrapping
- Autonomous Mobile Robotic Transport
- Robotic Handling
- Precision Packaging
- Conveyor System
The Vertical Rocket Cutting Machine (VRCM) is a Custom Engineered System that is made up on 3 primary elements. First is the automated production process. Second is the Vertical Rocket Cutting Machines. And finally, the Process Reject Station. This system was designed and built to produce a safe and efficient processing environment.
Features of this custom assembly system include:
- Material Handling
- Hydraulics
- Automated Reject system
- Robotic Product loading
- Precision Cutting
The objective of the custom crimp station was to create a machine that would secure the warhead in an air-tight package, without damaging the warhead so that it can be stored until it is ready for destruction. The combination of the CRG Automation custom crimp station and CRG Automation custom designed canisters achieved that objective.
Features of this custom assembly system include:
- Precision Crimping
- Hydraulics
- Reject Detection
- Robotic product loading & unloading
Each of the above case studies is a testament to the ingenuity of CRG Automation’s custom manufacturing solutions. Contact us today to discover how your current process can benefit from our custom assembly and manufacturing solutions, and get a free packaging systems assessment by submitting the form below. Tell us about your most challenging issues, and our technical field engineers will visit your facility to develop a custom manufacturing solution.
Contact us about our Packaging Systems Assessment
Contact
Explore each step of the CRG Automation process below to learn more about our custom assembly and automated manufacturing capabilities.
CRG Automation stays true to our proven process to design, build, and integrate custom manufacturing solutions to meet our customer’s assembly and packaging needs. Our process outlines the key steps we take to ensure each element of your industrial automation project is well managed along each step of the way.
Voice of the Customer
At CRG Automation we know that every custom manufacturing solution starts by listening to and understanding the customer.
Concept Development
This is where the team at CRG Automation springs into action to begin the process of developing a custom assembly or manufacturing solution.
Data Analysis
This step is to validate that the Problem Statement is accurate and all-encompassing of the current issues at hand. CRG Automation shares the information gathered from step one to gain mutual agreement on the Problem Statement to gain acceptance to move forward with the process of developing custom manufacturing solutions.
Prototyping
Solving problems that make most people want to bang their heads against a wall is where CRG Automation excels. With many custom manufacturing solutions under our belt, we are tasked with solving problems that others cannot.
Engineering
By calling on the power of our in-house engineering department, CRG Automation is able to maintain collaboration, control, and teamwork throughout the entire development process for all custom manufacturing solutions.
Procurement
Our supply chain team takes full advantage of our network of industry leading suppliers to ensure that parts and materials meet the quality specifications, availability, and timelines needed to fulfill the needs of our customers’ projects.
Fabrication & Assembly
Our team of experienced fabricators and technicians are involved with all CRG Automation custom manufacturing solutions from the beginning of the process. When it comes time for final assembly, they are experts on the project.
Production Line Process & Development
Once the system is built and wired, we begin running trials of the various components as well as the complete industrial automation system. During this trial phase, the system is developed by fine tuning the mechanical and control elements to ensure robust and reliable operation.
Testing
Before any CRG Automation custom engineered solutions leave our factory, we follow a vigorous testing protocol to ensure all performance and safety metrics are being met during a Factory Acceptance Test.
Shipping
CRG Automation will not ship out any custom designed solution until our confidence level is 100% that we have met or exceeded our customers’ expectations and performance metrics. It is only then that we put our logo on the solution and ship it out to another satisfied customer.
Site Installation & Commissioning
During this stage, CRG Automation ensures that all components are assembled and integrated properly and then we perform a Site Acceptance Test (SAT) to validate the system performs as it did during the FAT. CRG Automation also offers on-site training for operation, change over-parts and routine maintenance.
Custom Manufacturing Solutions
CRG Automation is a leading manufacturing company that specializes in providing custom solutions for your business. We understand that every industry has unique needs and our team of experts is dedicated to creating tailored manufacturing solutions that meet those needs. With state-of-the-art technology and advanced engineering, we are able to design, develop, and produce specialized components or products to fit your exact specifications. Our commitment to quality and efficiency has earned us a reputation for excellence in the industry. Whether it's for small-scale production or large-scale manufacturing, CRG Automation is the go-to choice for custom automated solutions.
Custom Assembly Systems
CRG Automation is a leading company in the manufacturing industry, specializing in creating custom assembly systems for various industries. With 20+ years of experience and a team of highly skilled engineers, we pride ourselves on designing and building custom assembly solutions that are tailored to our clients' specific needs. Our approach is customer-centric, where we work closely with our clients to understand their production processes and develop a solution that optimizes efficiency and productivity. From initial design to final installation and testing, our team ensures that every aspect of the assembly system meets the highest standards of quality and functionality. We are committed to providing our clients with innovative and reliable custom assembly systems that help them stay ahead in today's competitive market.
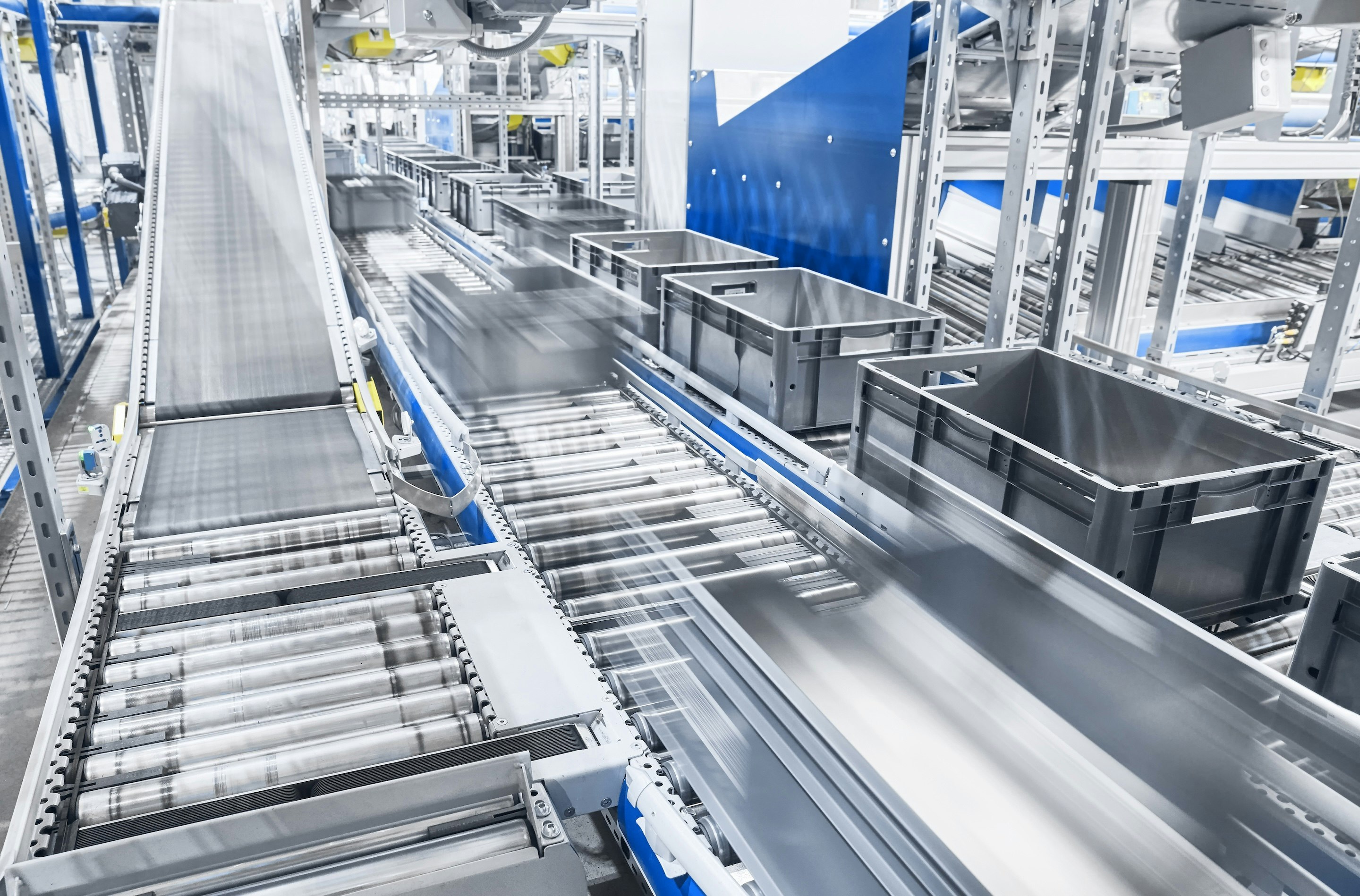
Our Process
At CRG Automation, we pride ourselves on our efficient and effective process of designing, building, and integrating custom automated manufacturing solutions for our clients. Our first step is to thoroughly understand our client's unique needs and specifications, as well as any challenges they are facing in their current production processes. From there, our experienced team of engineers and designers work to create a customized solution that not only meets our client's requirements but also optimizes efficiency and productivity. Once the design is finalized, our skilled technicians and builders bring the solution to life, paying close attention to quality and precision. Finally, our team ensures a smooth integration of the new solution into the client's existing systems, providing support and training to ensure a seamless transition. Our commitment to continuous improvement allows us to deliver innovative and cutting-edge solutions to help our clients stay ahead of the competition.