Custom Assembly & Solutions
Voice of the Customer
At CRG we know that every custom engineered solution starts by listening to and understanding the customer. To accomplish this, we execute the following steps:
As found condition assessment – it is very important to know the current process and situation to fully understand what solutions are needed in order to solve the customer’s problem. This is accomplished with a site visit and review of the current process from start to finish.
Key metrics review – as part of the as found condition assessment, a full review of the current key metrics is performed with the customer. Understanding the current performance metrics (through-put, efficiency, accuracy) is paramount in understanding the key areas that are performing at required performance rates and those that are underperforming.
Ideal State & Expectations – Where does the customer need to be? This is a crucial step in CRG fully understanding the desired outcome. This includes performance requirements, potential timelines, and other key factors needed for a custom engineered solution. This is key in developing the scope of work for the project.
Developing a Problem Statement – working in tangent with the customer, we complete a discovery process that will identify the customers issue and we use that information to develop a problem statement that will drive our Custom Engineered Solution process.
Concept Developement
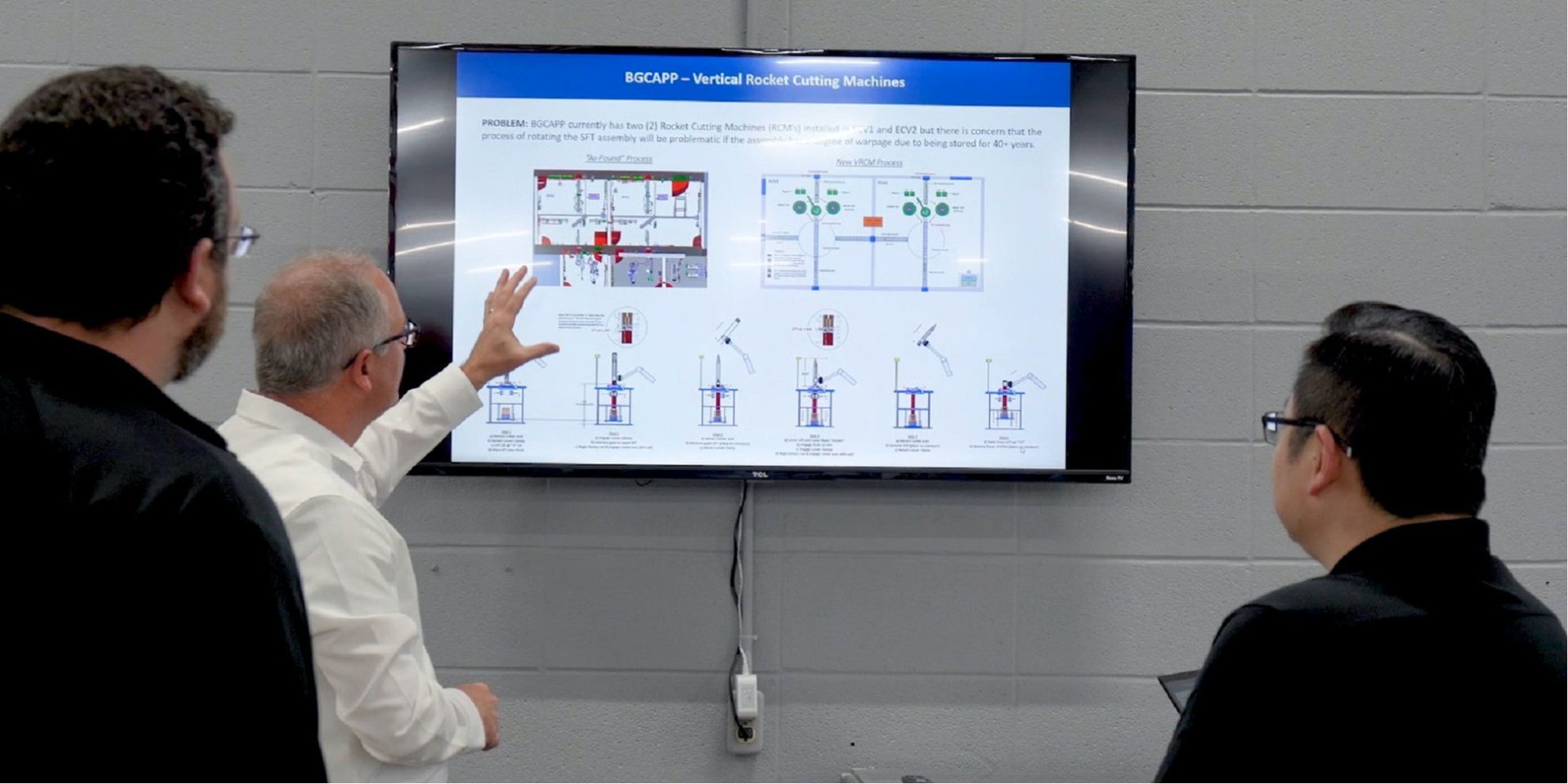
Ideation – this is the starting point where we pull our team together to review the voice of the customer and data analysis and start whiteboarding solution ideas. This team includes leaders from all relevant CRG departments as well as our partners who may offer unique perspectives and potential solutions.
Preliminary layout & process development – once the concept has been worked through and a solution has been developed, our engineering team develops the preliminary layout drawing.
Cost benefit analysis – at this point, CRG utilizes its team to develop a proposal that will outline cost in comparison to the projected ROI based on the increased key performance metrics as outlined in the data analysis stage. This is to ensure we are offering a solution that resolves their problem statement and provides value. That value can come in labor savings, increased output and production times and reduced overall production costs.
Risk Assessment – preparing for the unknown is critical in developing a custom engineered solution for our customers. CRG conducts a risk assessment for each custom engineered solution and shares that information with the customer. This ensures that we anticipate issues that could present themselves throughout the process and allows CRG and the customer to be prepared in the event these issues arise. Preparation on the front end reduces delays and added costs throughout the process.
Data Analysis
This step is to validate that the Problem Statement is accurate and all-encompassing of the custom engineered solution. CRG shares the information gathered from step one to gain mutual agreement on the Problem Statement to gain acceptance to move forward with the process.
Review of Historical Performance – verify that information gathered is still accurate pertaining to key metrics of their current process.
Review Current Issues & Constraints – review and verify with the customer the identified issues and constraints from their current process and ensure that all relevant information has been communicated from the customer to CRG (product sizes, throughput speed, efficiency and accuracy).
Validate Key Metrics – review desired outcome and key performance metrics that will be measured for the success of fulfilling the customer’s problem statement.
Prototyping
Solving problems that make most people want to bang their heads against a wall is where CRG excels. With many custom engineered solutions, we are tasked with solving problems that others cannot.

Design/Build prototypes – our team of engineers, fabricators, builders, and technicians are able to utilize our 40k sq. ft. shop to design and build prototypes for the unique solutions that our customers need.
Reduce risk – by designing prototypes for our customers, we are able to demonstrate proof of concept to them early in the development of the solution to reduce risk and uncertainty.
Refine Concepts into Practice – the utilization of prototypes allows CRG to refine our concepts, so we have the ability to offer proven solutions to the customers custom engineered needs.
Identify Additional Opportunities – while executing our prototype and POC phase, it is not uncommon for CRG to identify additional opportunities to improve on our solution or the customer’s current process. This offers more value as a customer of CRG by not only solving the customer’s need, but also improving their overall system process.
Engineering
By calling on the power of our in-house engineering department, CRG is able to maintain collaboration, control, and teamwork throughout the entire custom engineering solution process.
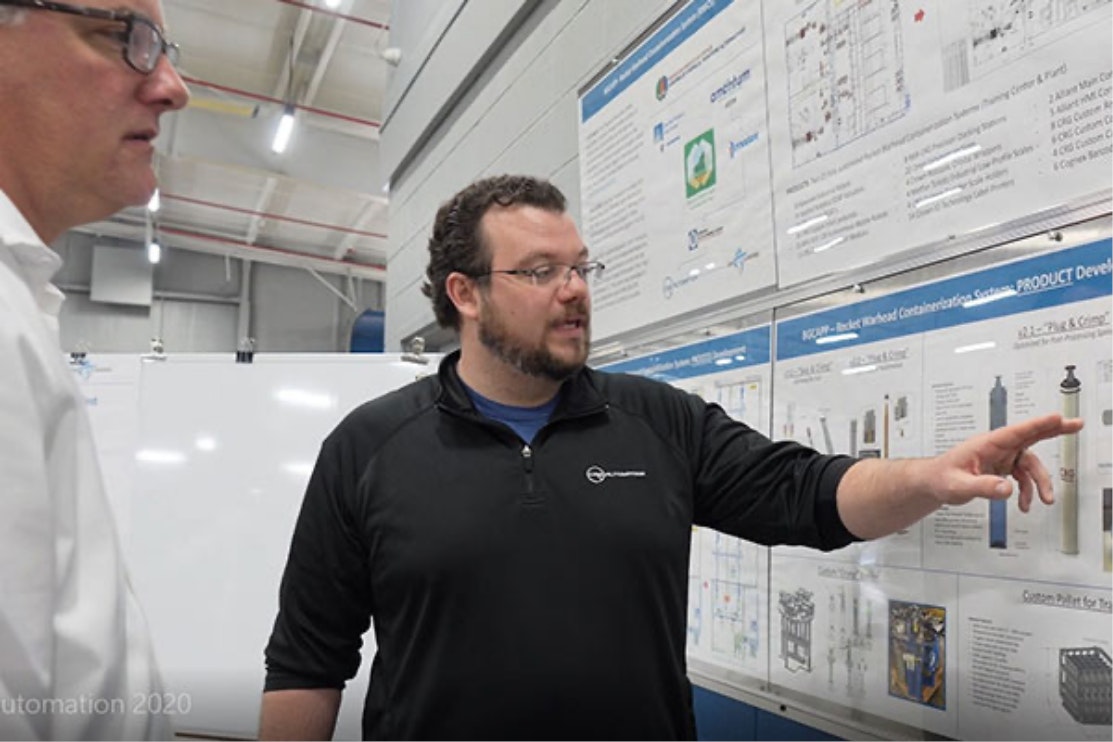
Mechanical Engineering – our mechanical engineers work together to help develop solutions to the most complex customer issues. They produce drawings from the concept stage to the highly detailed individual parts of the solutions. CRG can also produce renderings, 3D graphics and perform 3D scanning of the customer’s facility.
Electrical Engineers – our experienced team of electrical engineers are ready to help design the custom solutions our customers need. With extensive experience in servos, gearboxes, robotic programming and electrical diagraming, they can design a system to meet your needs whether it be speed, accuracy, efficiency or all the above.
Controls Engineering – with experience with all major control platforms, CRG is positioned to solve your custom control needs. Whether it is integrating systems to communicate with each other, programing HMIs, designing safety controls or building complete control cabinets, CRG can solve your custom control issues.
Manuals – all custom engineered solutions come with a complete user manual in both print and digital forms.
Quality Requirements – safety and quality are paramount with CRG and we take great effort to ensure that our solutions meet or exceed industry safety standards and are built to operate at repeatable performance specifications for years of reliable service. In addition, we work closely with our customers to ensure any specific safety requirements are engineered into the solution and our CRG warranty covers our equipment to offer peace of mind, and confidence.
Procurement
Our supply chain team takes full advantage of our network of industry leading suppliers to ensure that parts and materials meet the quality specifications, availability, and timelines needed to fulfill the needs of our customers projects.
In addition to the solution build, our supply chain team is standing by for replacement parts on all CRG engineered and built machines.
Fabrication & Assembly
Our team of experienced fabricators and technicians are involved with all CRG custom engineered solutions from the beginning of the process, so when it comes time for final assembly, they are experts on the project. From welding, fabrication of specialty parts, programing HMIs, and building control panels, CRG ensures our equipment is top quality for reliable performance and durability.
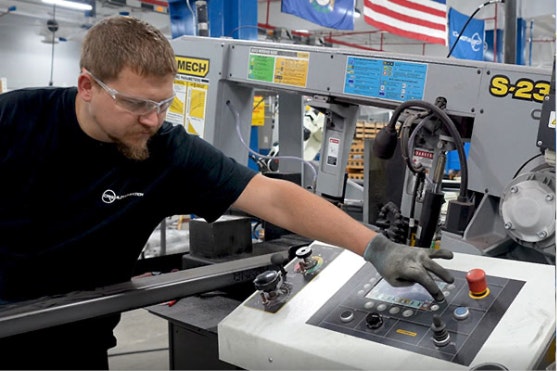
Production Line Process & Development
Once the system is built and installed/wired we begin running trials of the various components as well as the complete system. During this trial phase, the system is developed by fine tuning the mechanical and control elements (sensors, speeds, routines etc.) to ensure robust and reliable operation.
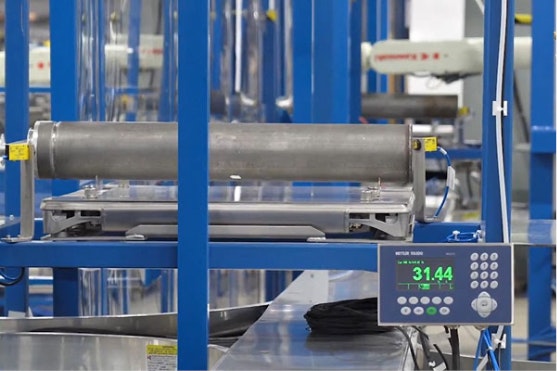
Testing
Before any CRG custom engineered solutions leave our factory, we follow a vigorous testing protocol to ensure all performance and safety metrics are being met during a Factory Acceptance Test. This FAT stage includes performance testing and a failure mode and actions review.

Performance Testing – the first phase of testing after the assembly is complete is the overall performance test. This is conducted at CRG and tests to ensure that all components, safeties and controls are functioning within the specifications outlined by the customer.
Failure Modes and Actions Review –– our systems are designed to not only handle your products within their specification ranges but can also be designed to handle known failure or reject operations based on out-of-specification products, further reducing downtime and unnecessary operator intervention into your automated solution.
Factory Acceptance Testing – the final phase of testing occurs prior to shipping the solution to the customer. The FAT is conducted at CRG, to the customer’s specific metrics with them in attendance. The FAT is the designated step to show the customer that the solution will perform as specified, all controls are programmed and functioning, all safety components are active, and we walk through the change-over process if applicable. Once complete and the system has passed, our customer will sign off and we will prepare to ship it out to them.
Shipping
It has been a very detailed journey to get this point, but CRG will not ship out any custom designed solution until our confidence level is 100% that we have met or exceeded our customers’ expectations and performance metrics. It is only then that we put our logo on the solution and ship it out to another satisfied customer.
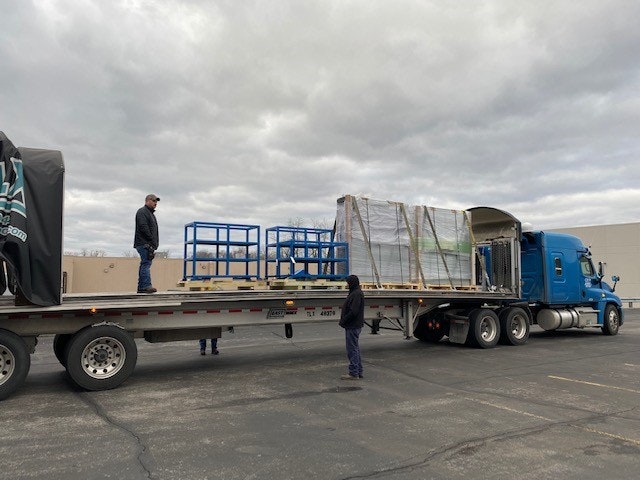
Site Installation & Commisioning
This is the final stage of the custom engineered solution process. At this stage we offer for our technicians to manage and over see the on-site installation and commissioning. During this stage, CRG ensures that all components are assembled and integrated properly and then we perform a Site Acceptance Test (SAT) to validate the system performs as it did during the FAT. CRG also offers on-site training for operation, change over-parts and routine maintenance.