Automatic Packaging Systems
PACKAGING MACHINERY
It is important to understand that when discussing packaging systems that there are really two different, but integrated packaging systems. The first system is the packaging of the commodity into its presentation packaging, also known as the primary package. This is the form that the customer sees when the product is on display in its saleable form. If it is a canned beverage it may be in groups of six or 12 for example, that are ready to be put directly on a shelf. The other form of packaging, the secondary packaging, is intended to safely contain the primary packaged product in bulk so that it can be transported (usually by truck) to a distribution warehouse, or even the warehouse portion of a retail center, like a grocery store for example. This secondary packaging generally needs to be more heavy duty to handle the rigors of transport. Even though there are different requirements for these two stages of packaging they need to be treated as an integrated whole. This approach ensures that there will be seamless transitions between the various steps required for effective packaging. Both packaging requirements benefit from automation by providing more consistent results, lower loss and flexibility to expand.
CUSTOM PACKAGING
Primary packaging is designed with the consumer in mind. The basic steps in this part of the packaging process may include filling the container: whether it is a beverage; a powder; or some other bulk food product. This filled container may be the primary package itself, or it may go into the primary package. No matter how it is done, if it is a consumer good, it is also subject to specific labeling rules to ensure that the ultimate user of the product is aware of the contents of the product, manufacture date, expiration date, manufacturer’s name and so on. Choices are made about the robustness of the packaging, color, placement of logos, etc. These choices affect decisions about how the transport packaging is designed. A flimsy card stock container may require a more robust cardboard for the secondary packaging for example. Bagged and sealed packaging, like potato chips, may expand considerably during transit, especially if packaged near sea level, but transported to a higher elevation for sale. This may require extra room for expansion during transit. These are just a few examples of the kinds of issues that must be taken into consideration at the consumer package level.
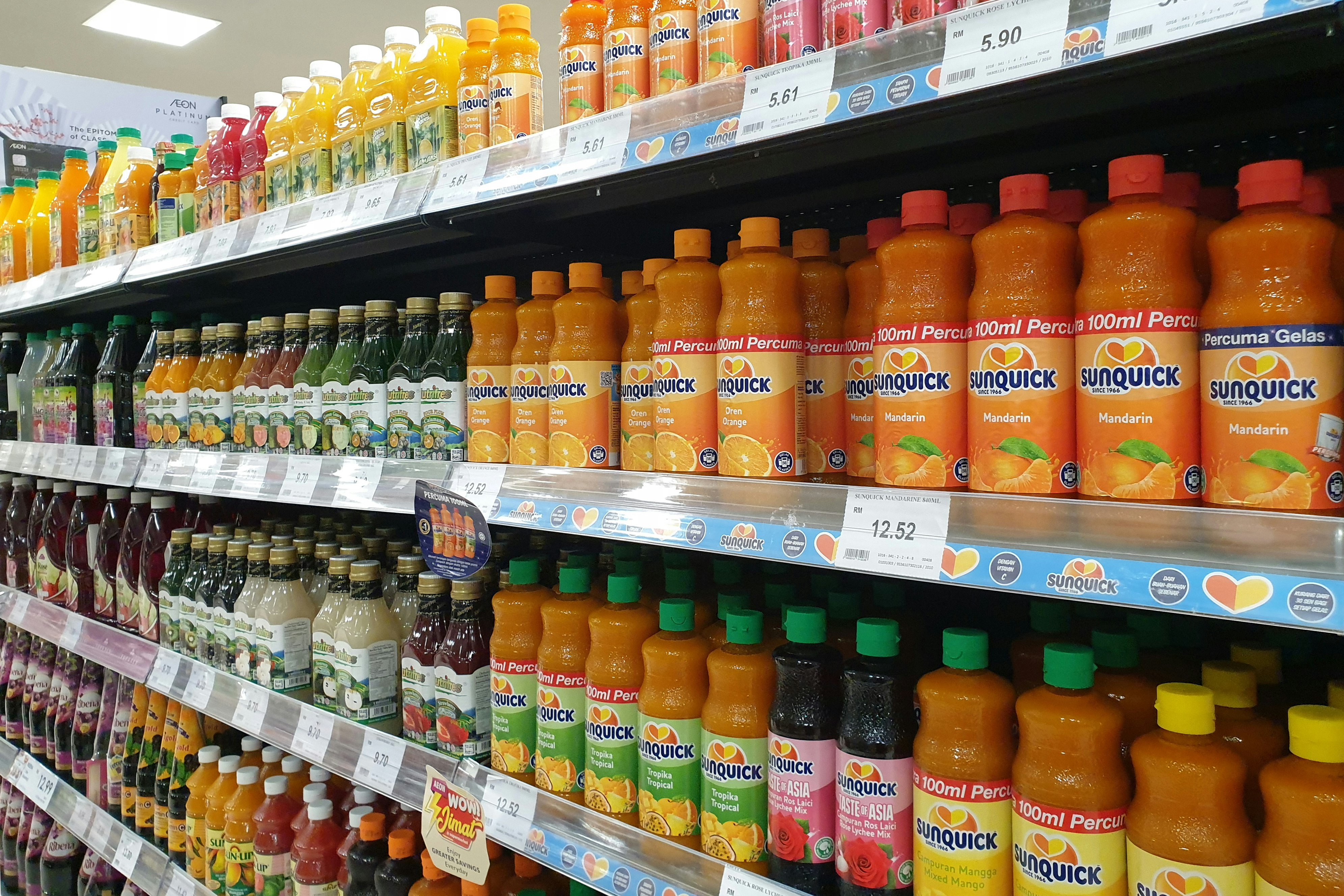
AUTOMATION AND STRETCH WRAPPING
Once the retail product packaging has been well defined, then the secondary packaging can be developed. The job of this packaging is to ensure that the primary package and the associated product arrives safely at the destination in pristine condition, with no damage to the primary packaging or its contents. These requirements are critical to a good finished product and is one more reason to have the entire packaging system designed by a single vendor. This has to take into account that bulk handling equipment, like fork trucks or pallet jacks will likely be used to move product. Transit via truck may be subject to constant, low-level vibration which may have the potential to abrade the labeling and reduce the quality of the primary package, or its contents. The dimensions of the primary package will determine, in part, the size of the secondary packaging. Slight modifications to the primary package, could save weight and cost for the secondary package. For these reasons, it is important that the packaging decisions are a shared responsibility by both the product designers and the packaging designers.
It is common to use stretch wrap to bundle several packages together for transport. Stretch wrap, when properly designed and implemented provides a secure way to stack larger secondary packaging on a pallet and to ensure that the boxes and the pallet will stay together during handling. Stretch wrap systems can be either partially or fully automated. Regardless of the type, a poorly balanced stretch wrap system can lead to collapsing of the load and loss of product during transit or storage. Once the product has been delivered, the stretch wrap is cut away and the packaged product is stored in the warehouse. Box cutters are often used to remove the stretch wrap and also to remove the secondary packaging. These have the potential to score the primary packaging if not used carefully. These are just a few of the considerations that need to be taken into account to ensure safe delivery of the finished product onto the retail shelf.
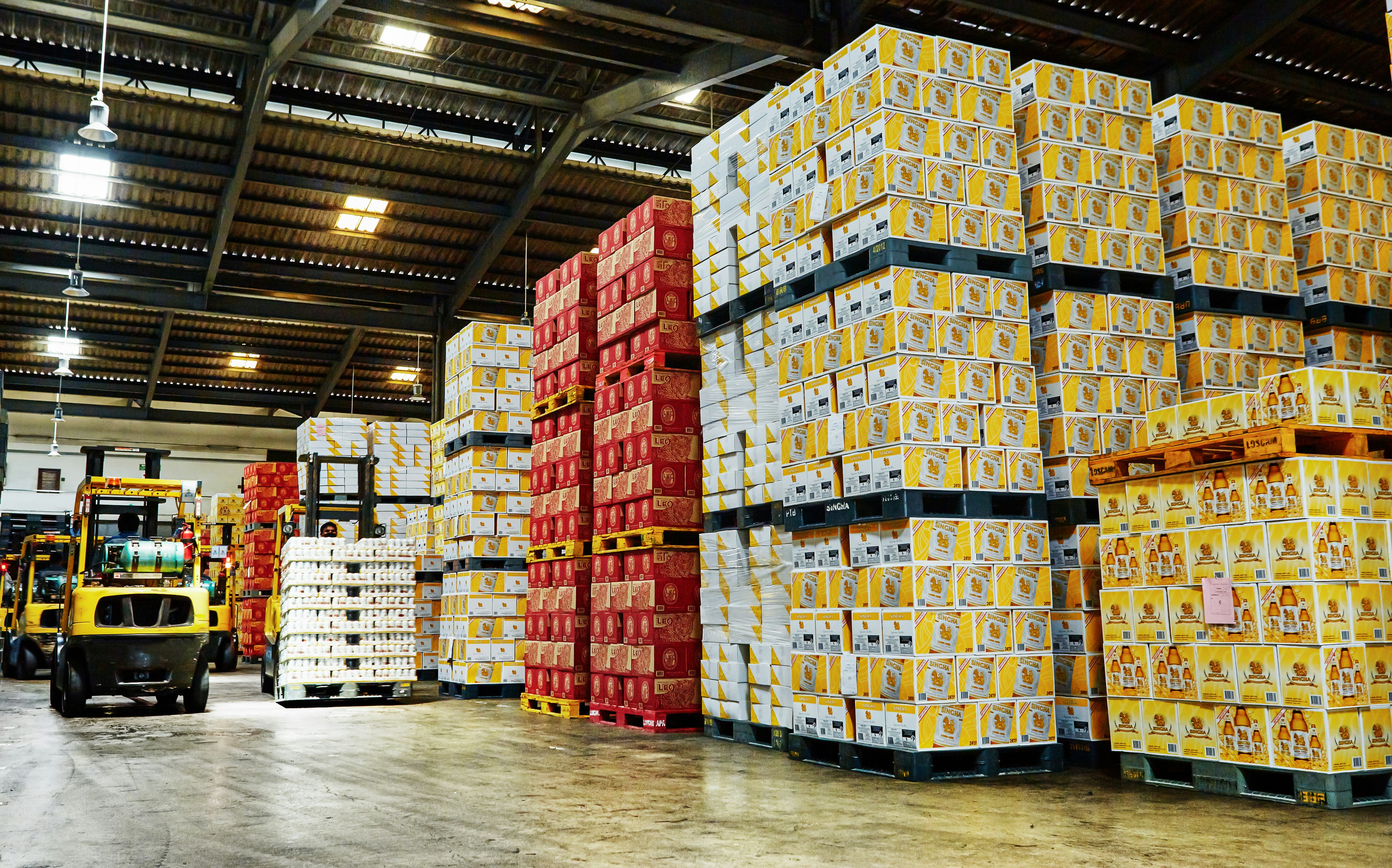
THE COMPLETE PACKAGING SOLUTION
The purpose of an integrated packaging system is to ensure the journey from a packaged product to its final placement on the shelf for purchase is executed flawlessly. It is a task that requires expertise and attention to detail. Fortunately many companies, like CRG Automation, specialize in these handling and packaging issues on a regular basis. Given the final product size, weight and design, CRG can work with the customer to avoid a lot of the pitfalls mentioned above. From glassware to snack packaging, CRG has developed efficient equipment designed to handle both primary and secondary packaging to reduce breakage, potential leaks, and damage due to handling. They can ensure that your packaging needs will be met safely, efficiently and economically.