CRG Technologies Becomes CRG Automation to Reflect Expanded Automation Focus
Company completes full renovation of 40,000-square-foot headquarters
May 2020 — LOUISVILLE, KENTUCKY —CRG Technologies announced today the company’s name has been changed to CRG Automation. The move signals the 20-year-old company’s expansion over the past several years to focus on solving automation problems for its large customer base, which includes Coca-Cola, Reynolds, Kellogg’s and Kraft.
“This is more than a name change,” said James DeSmet, the president of CRG Automation who previously held top engineering and manufacturing roles with fan and light maker Big Ass Fans and General Electric. “CRG Automation’s quality work, attention to detail and flexibility have earned us the trust of the world’s leading companies. We’re proud to now officially reflect how we’ve been solving our customers’ toughest automation challenges with custom solutions, not out-of-the-box bandages.”
CRG Automation has long specialized in developing, upgrading and optimizing packaging and process equipment for the food, beverage and consumer products industries. The company’s staff includes mechanical, project, process and electrical engineers, as well as machinists and electrical controls specialists.
In recent years, the company expanded its business lines to include the development of custom automation solutions, earning recognition including selection by Fanuc & Kawasaki Robotics for inclusion in their Preferred Integrator Networks. While CRG Automation continues to develop and offer cartoners, case-packers and other secondary equipment, the company now also serves its customers with advanced solutions, including robotic integrations.
CRG Automation’s 40,000-square-foot headquarters in Louisville, Kentucky, features a full controls and machine shop. The facility has also recently been renovated to expand floor space, offering the space to build complete proofs of concept and set up and conduct performance testing for full packaging and processing lines.
“Our business and its 20-year legacy of innovation is built on understanding our customers’ pain-points — the problems that keep managers awake at night — like how to reduce staff turnover on the most back-breaking work,” DeSmet said. “We’ve redesigned our facility to be able to completely replicate assembly lines and workspaces, so we can experience the issues first-hand and devise long-lasting solutions. We put our facility to work for our customers every day.”
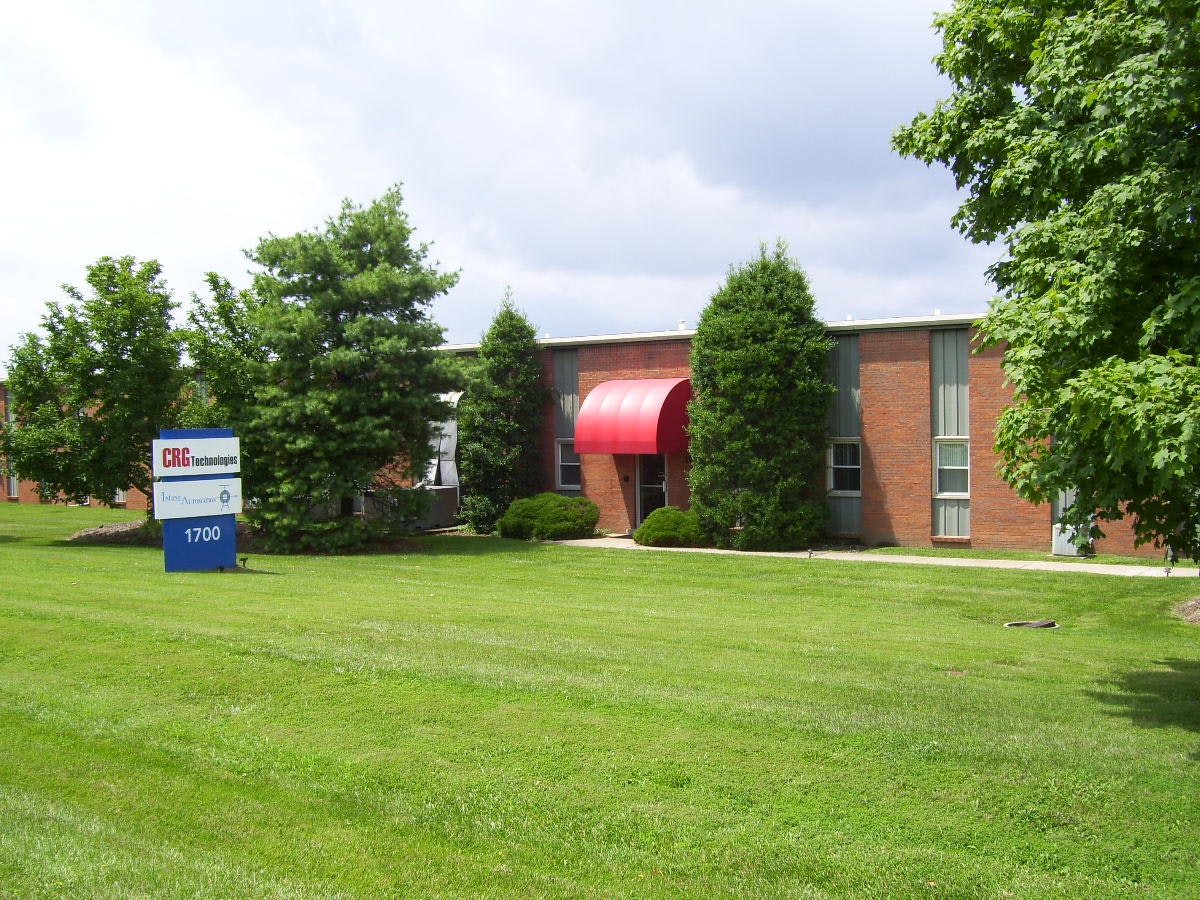
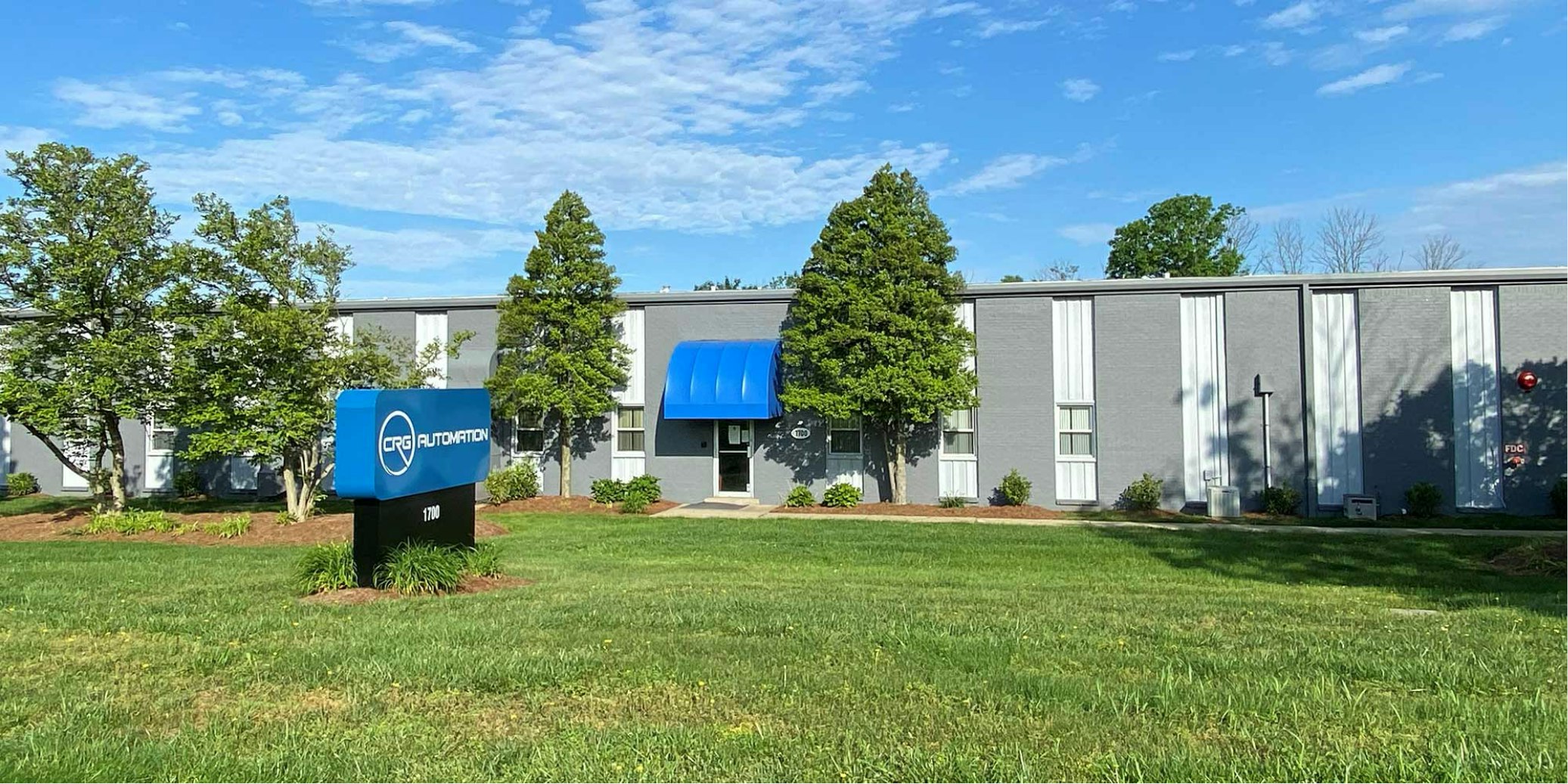
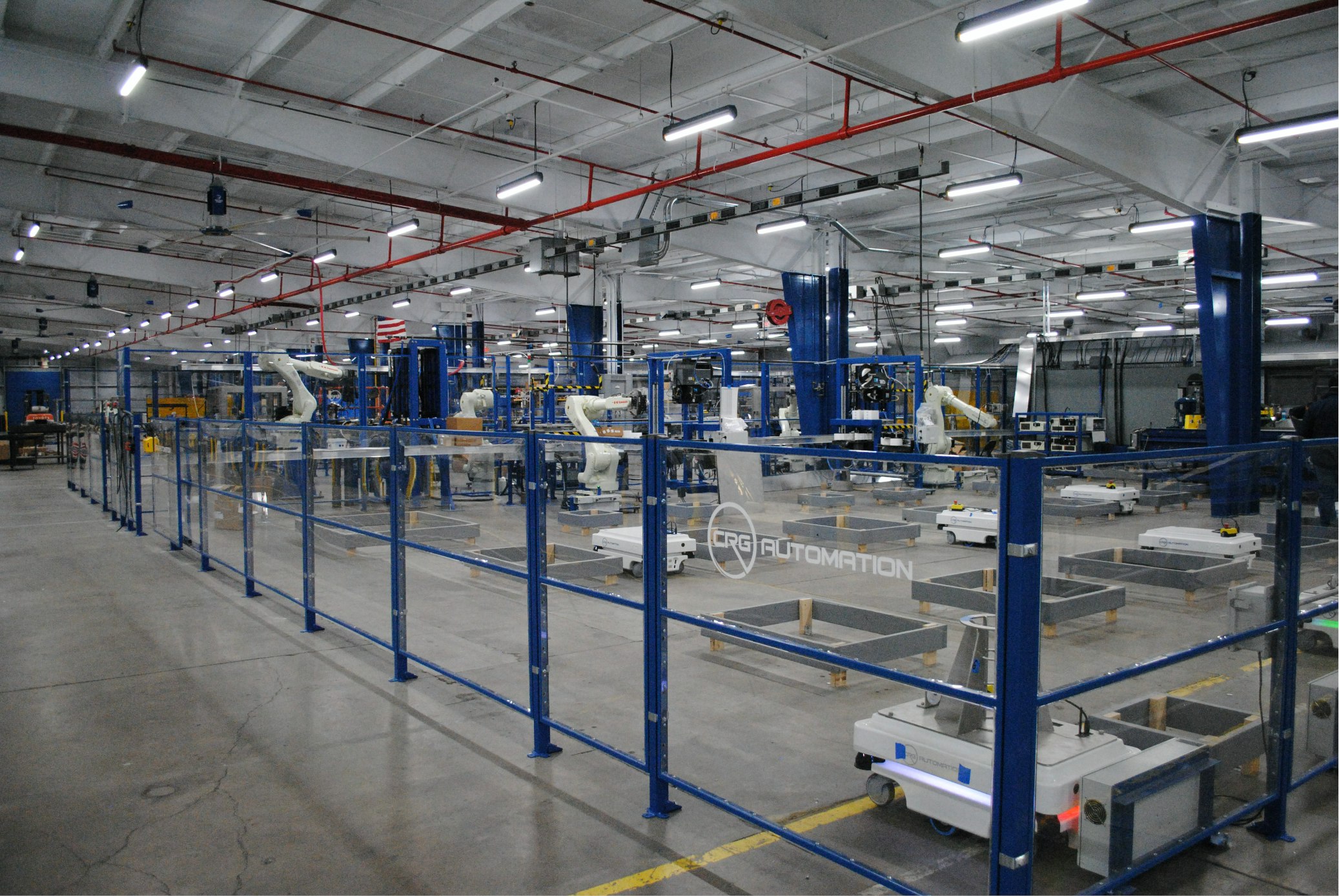