Factors to Consider for Conveyor Systems
For a lot of industrial packaging equipment, the conveyor system is the motive force. It defines the process flow both in terms of units as well as what operations occur and where. Since even small inefficiencies multiply quickly on fast-moving equipment, it’s worthwhile spending time to learn about the types of situations that could arise in the development stages of designing a conveyor system. What follows is a sort of check list of things that you want to make sure you’ve covered before green lighting a project.
SIZING YOUR CONVEYOR SYSTEM
This first step is perhaps the most obvious, but what’s surprising is the number of ways in which the basic characteristics of the item to be conveyed can influence the design. The first step is to know your product. What are the dimensions, how much does it weigh, what is the density, where is its center of gravity, is there room in the container for the contents to shift, how many units at a time need to be supported by each section of the conveyor, if there is a backup how much space needs to be set aside as an accumulator?
Once all the knowns are defined, the path of product through the handling equipment can be nailed down more precisely, being sure to leave clearance where needed. If product is moving up or down, that can affect the energy requirements. Any changes in the center of gravity can become important, especially if the contents are prone to shifting. Make sure that the conveyor is robust enough to handle the expected weight based on throughout.
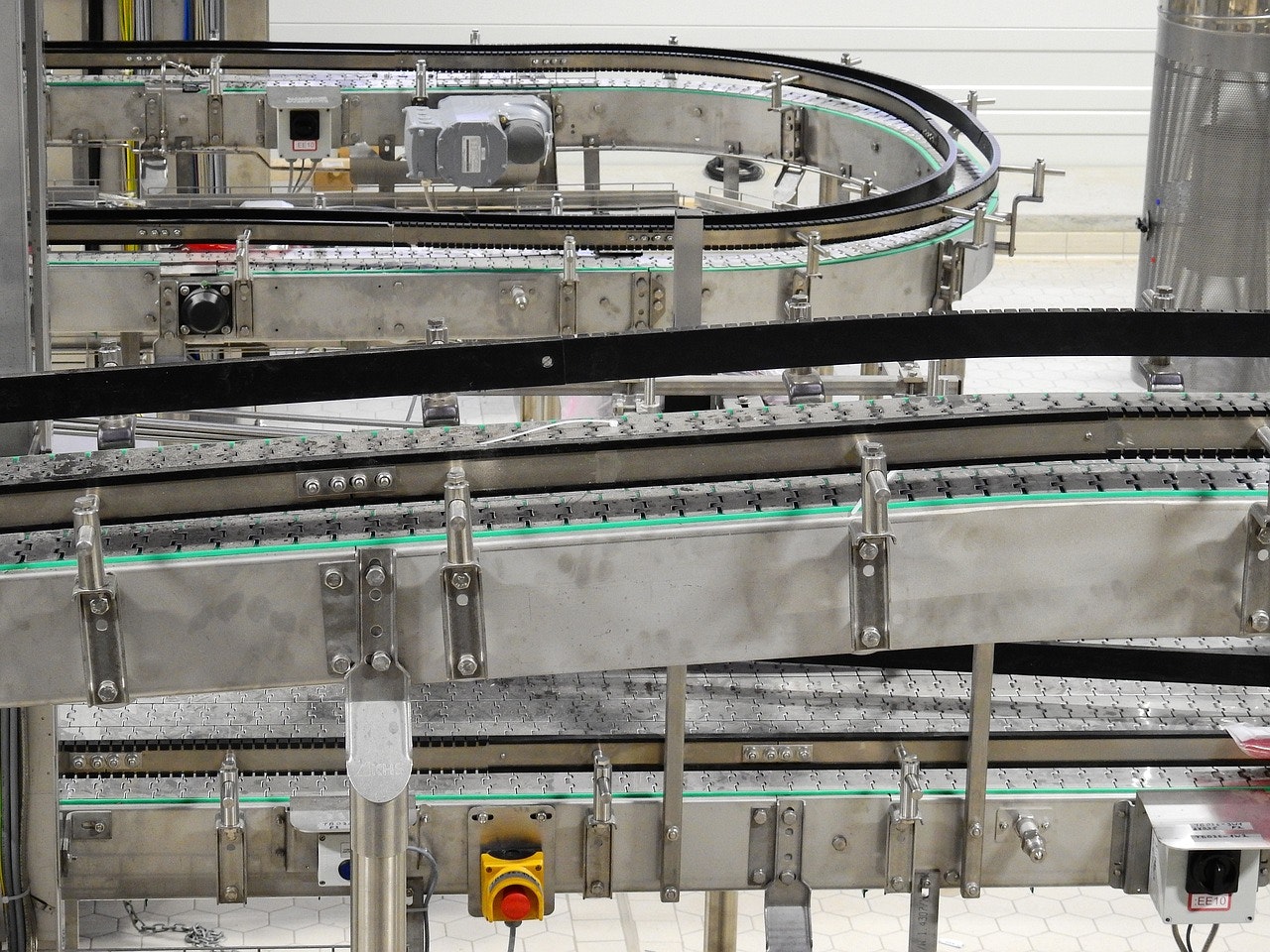
CONVEYOR TYPES
There are may types of conveyor transport mechanisms. Some are powered and others rely on gravity. If you are handling food products, there may be requirements for wash-down capability. Belt conveyors, rollers, chain, even pneumatic conveyors are available. The key things to look for are compatibility with any applicable regulations, the coefficient of friction between the surface and the product, and durability – especially for belt conveyors.
It may be that several different conveyor types should be used based on different needs in different sections of the conveyor system. Especially if the character of the product changes as it travels through the manufacturing process. There may be steps that require spraying, dehydration, singulation, heating, chilling or filling that change the product or produce debris that must be managed.
WORKING WITH A CONVEYOR LAYOUT
This can be a tricky part of the process because rather than focusing on the conveyor system itself, it requires imagining the working area immediately surrounding the conveyor footprint. For this process a plan view of the proposed layout should be combined with a plan view of the proposed location for the equipment.
With that drawing in hand, think through all of the activities that need to take place in the vicinity of the conveyor to be sure that there are no interferences. Try and think of everything, no matter how small. Questions you might ask include: is that area currently being used by pallet jacks, forklifts or other equipment? Do you need access to load up consumables like cartons? Are there access panels that need room to swing out to give access to clear back-ups? In short, think about all of the activity that will be going on around this new piece of equipment and make sure there are no potential interferences or pinch points.
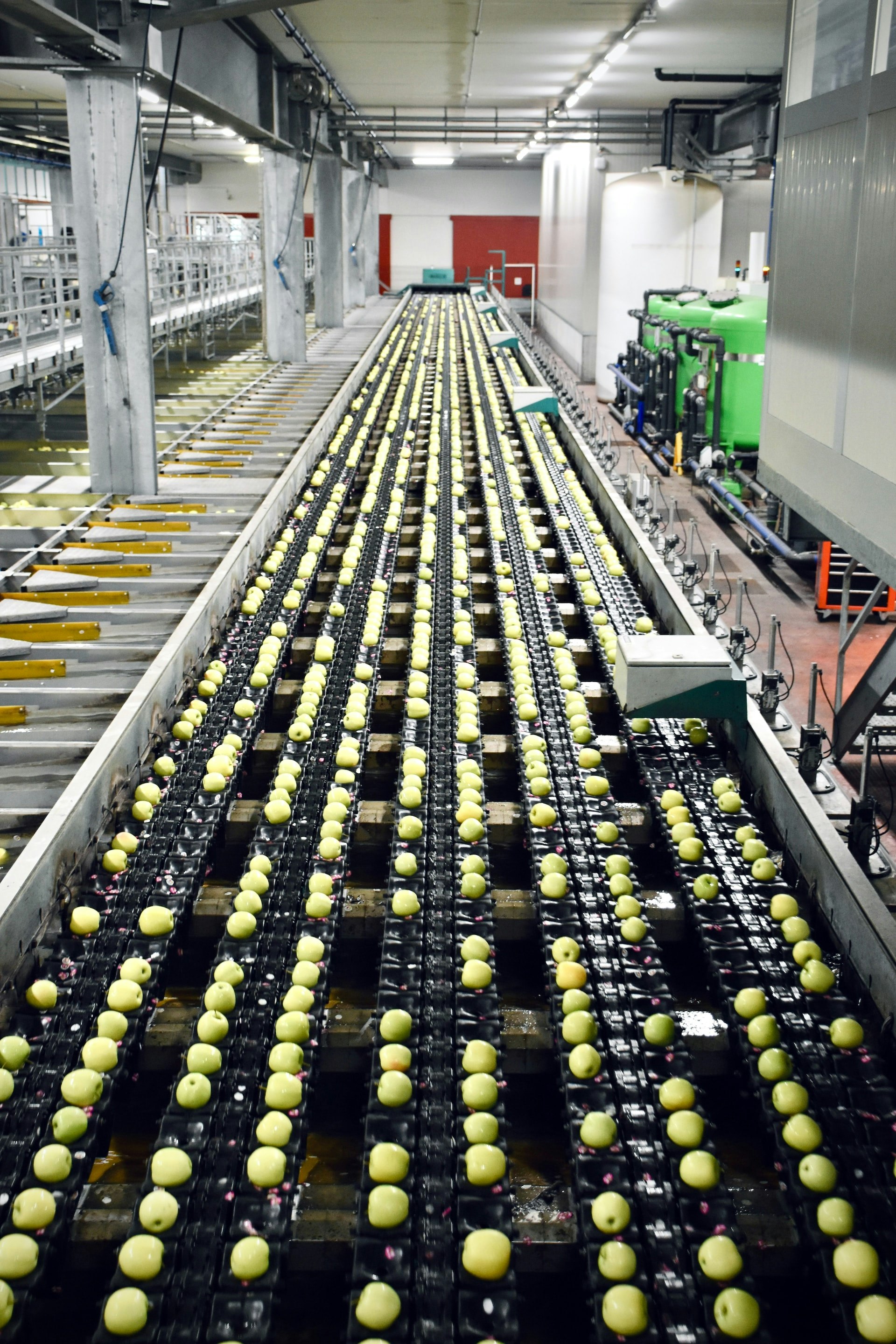
CONVEYOR SAFETY
Operational safety is usually automatically assumed. That is, all parties can agree that they want safe operation. The trick is really about implementation. A safe installation and operation by its very nature is more economical and efficient by reducing accidents, downtime, root cause analysis and safe restarts. Some of the obvious safety features include signage, guards, proximity warning devices, light curtains, fall protection and safety interlocks. Also, don’t discount the value of ergonomic design that makes it easier to avoid accidents in the first place. Where a lot of safety systems fall short is in the execution. It is important to have regular safety drills. Not only does this help keep safety uppermost in everyone’s minds, and validate that safety systems are working, when a safety situation arises, operators will already know how to react. This saves critical time in activating e-Stops, handling spills, executing safe shutdowns and so forth. Frankly, a safety system, like a fire extinguisher is no good, if you don’t know how to use it.
MAINTAINING YOUR CONVEYOR SYSTEM
Make sure to plan for maintenance and cleaning. Wear points might need lubrication or occasional replacement. Certain areas may accumulate particulates, shavings or other debris that poses a slipping or fire hazard. You want to make sure that easy access to these maintenance points is maintained. This access is often cut-off or restricted due to design. It’s not unusual to save the routing of conduit, piping, and location of work platforms as the final step in a design. Without forethought this can lead to such nuisance items as conduit that is a tripping hazard, or must be removed to access a maintenance panel. With an eye toward safe and easy access for maintenance, countless hours can be saved by making access for maintenance or servicing a routine, easy activity rather than an onerous one.
FUTUREPROOFING
Lastly, it’s practically a given that the conveyor system that is installed today will not be the conveyor system that you will need five years from now. It’s always a good idea to have in mind what sort of changes you might anticipate. This is not an exact science but there are some common themes. Some typical changes include, a higher run rate, different package sizes, product change (i.e. from a liquid to a powder form), changes to packaging and so on, depending on the type of product being handled. It’s good to have these discussions early on in the design. Higher run rates, for example may increase back-ups and actually reduce efficiency if they haven’t been thought about ahead of time. If this is the sort of thing that you realistically may need, making the decision earlier in the design cycle saves money in the long term.