What You Need to Know About Automated Inspection
The Role of Automated Inspection
Watching any sort of automated assembly operation can be mesmerizing. The repetitive precision of operations performed again and again seems improbable and fascinating. Part of the “magic” of the automated operation is often not overtly visible. Embedded within the equipment, at certain critical locations are inspection stations that are constantly giving feedback to the equipment to let each operation know that it is on-track with its intended function. Without these inspection stations each station would be operating in an “open-loop” mode. This would be like driving your car without a speedometer or any rear-view mirrors. These simple device contain a wealth of information to help you safely operate your vehicle in all kinds of situations. Having the mirrors and speedometer constitutes a “closed loop” system in which you are constantly receiving information that allows you to make small adjustments on the fly to ensure that your vehicle stays on track and out of trouble. Automated inspection operates in much the same way, and can even “hit the brakes” if needed should things get out of control.
Automated Inspection Principles
The trick with any inspection system is to figure out how to make each step of the process foolproof against errors. This is usually as much an art as a science and brings out the creative nature of control systems designers. The objective is to put just enough feedback into the system to achieve a consistent result and to capture any out-of-spec condition. As an example, a common process would be something like filling up a cereal box with the correct amount of product. This problem has been solved a long time ago using a bag forming machine surrounding a dispenser tube that releases a certain weight of cereal into the tube and then seals the bag and cuts it off at the right length. Here’s a short You Tube video that shows this operation of cereal packaging . Note that there are references to a weighing station and an end of line inspection that checks for packages that don’t meet the weight, the physical box requirements or that have metal contaminants. This is obviously a very mature process since it is only checking the variables that are most critical. In addition, aside from the weighing station at the start of the process, nothing else needs checking until the very end of the process.
The previous paragraph referenced weighing stations, and testing for metal contaminants. If you start thinking about automating inspection, there are potentially a lot or things that could produce unsatisfactory product if they weren’t monitored. Examples could include, partial fill of liquid in a container, package not properly sealed, food product without proper temperature control and so on. The design engineer has a wide variety of sensors at their disposal; thermometers, laser measuring devices, and an array of optical sensors to perform in situ measurement based on their experience and the product being handled. Each automated process will likely have some unique aspect to it and this is where packaging expertise can save time and money in all stages of the process.
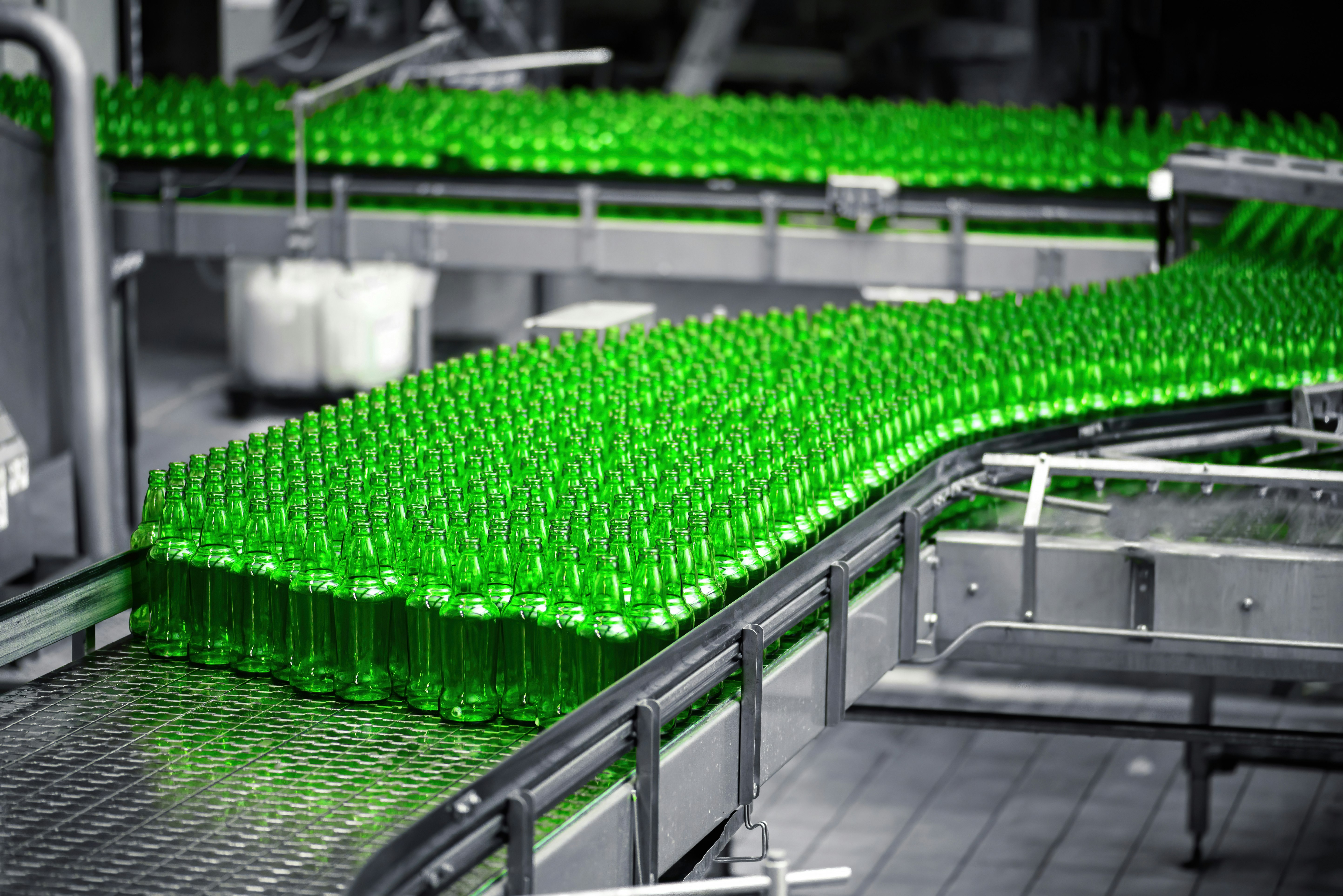
Does Machine Learning Play a Part
There had been a lot of press recently about the power of Machine Learning (ML). Like all fairly new concepts, this one is likely to be at least a little confusing to most people. The concept is straightforward: if you would like your equipment to be able to recognize a truck, you can feed it thousands, or millions of images of trucks from all angles, lighting conditions, colors and brands. Once it has absorbed this information, you can show it a picture of a truck that it hasn’t seen before, ask it, “Is this a truck?” and it should answer, “Yes”. How does this apply to inspection? The theory is that if you similarly fed thousands of images of your assembly process into a computer, then you could ask the computer, “Does this process look right?” at any stage of the process and as long as it kept saying, “Yes”, then the process could continue. This is part of the general thought across technology industries that some of the new fresh-from-the-lab processes: Artificial intelligence, Chat GPT, Machine learning, Neural networks and so forth will obsolete existing processes and disrupt the technology companies that they were supposed to help. Not to say that some good things may come from these explorations, but the probability that ML, as I’ve described it here, would take the place of automated inspection is likely to be off base for this application. And here is why.
The ML process has two major drawbacks. First, it is very time intensive to program. And second, it can only learn a generalized version of an assembly process, rather than the specifics of your particular process. To address the elephant in the room, for now, ML is more lab curiosity than practical solution. After all, when defining a manufacturing process and inspection points, these usually require very specific values. The targets are clear and the error bands are well-defined. This is the exact opposite of the ML process. There does not appear to be any specific use case that is compelling for ML in the automated inspection space.
Inspection Trends
In contrast to the Machine Learning situation, there has been a long-developing trend in the inspection world; and that is the use of high speed cameras for inspection. As mentioned before, most processes have specific target values they are try to hit. What has helped to grow the optical inspection market is higher resolution cameras and more sophisticated 3D CAD modeling. This has allowed for engineers to create a model of the perfect part (a beverage can top for example). It is easy to identify the critical areas and tolerances on the CAD model and the programming can take into account the orientation of the can top to easily match the orientation of the image of the model against the real part.
Optical systems are very versatile; able to detect irregular labels, read barcodes, capture statistical failure data, determine if parts are properly positioned, count the number of units on a conveyor, detect different parts based on outline and so much more. They have generally replaced mechanical systems like limit switches, mechanical counters, detectors for part orientation and monitoring of pallet stacking processes. These types of cameras can work in a variety of lighting conditions and also be mounted on robotic arms in order to do bin-picking operations for example. These cameras are more costly than simple limit switches or simple go/no-go control gates, plus they require programming. However the cost is outweighed by their versatility and their compact size allows for their use in a variety of applications. Given the added capability, speed and versatility, this is still a fast growing part of the inspection market and one that is worth exploring.
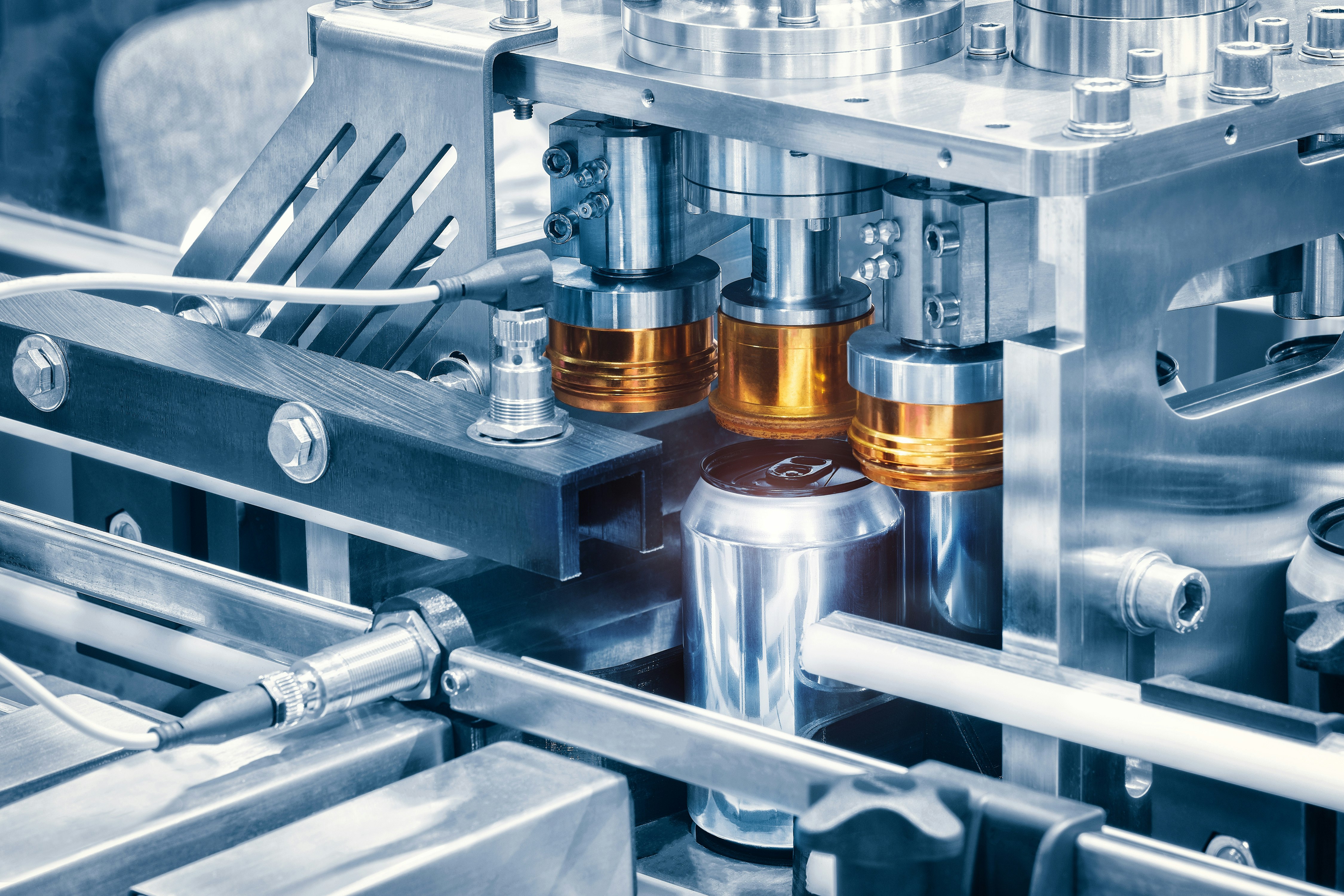